Balancing Complex Design and Cost-Conscious Engineering For Optimized Component Manufacturing
The intricate process of engineering effective, efficient metal stamping tooling relies on a careful balance between customer needs, cost-efficiency, and the functionality of the tool. Although the complexity of the part is a main factor in the cost of tooling, other customer inputs must also be taken into account to design tooling that will satisfy the unique, multi-faced needs of each part; these include estimated annual usage (EAU), product lifecycle, tool lead time, and production rates. Numerous tool steels are available, allowing the tool to be built for longevity, and there are also coatings for punches and dies.
The tool itself can be designed for high-volume capability to last for years, or it can be designed with reduced volume capability at a lower cost, depending on forecasted demand (referred to as “dynamic tools” at Lutco). The most critical priority is providing the right tool for the job; The design needs for a tool producing 1,000,000 parts over the next 10 years differ significantly from those for a tool that will manufacture 5,000 pieces over the next 3 years.
Dynamic Tooling: Lower Cost, Right-Sized Capacity Solutions
Dynamic tooling at Lutco represents a strategic approach to metal stamping, offering lower cost and reduced capacity solutions. This concept is ideal for projects with forecasted lower volume production, enabling clients to invest in tooling that aligns with their specific demands without the burden of high initial costs.
Dynamic tools are designed with a focus on efficiency and adaptability but may have a shorter lifespan compared to high-volume tools. They are particularly advantageous for short-term projects, prototype testing, or where market demand is uncertain. The benefits include cost savings and flexibility, while the primary disadvantage is the potential need for more frequent replacement or upgrade compared to high-volume counterparts.
Progressive Tooling Means Multi-Tasking with Precision
Progressive tools can perform several operations in one setup, including coining, drawing, punching, shearing, and even threading. These operations deform the raw material at different stations using an automatic feeder in a reciprocating press. The cost of the tool is heavily influenced by the required geometric features of the final part.
The most important element of tool design is the expertise and experience one must have to balance the cost of the tooling with the total volume of parts to be manufactured for the lifecycle of the part, thus maximizing ROI on the tooling investment. With a full spectrum of tool steels and coatings available, the right tool can be designed at the right price— by the right engineer.
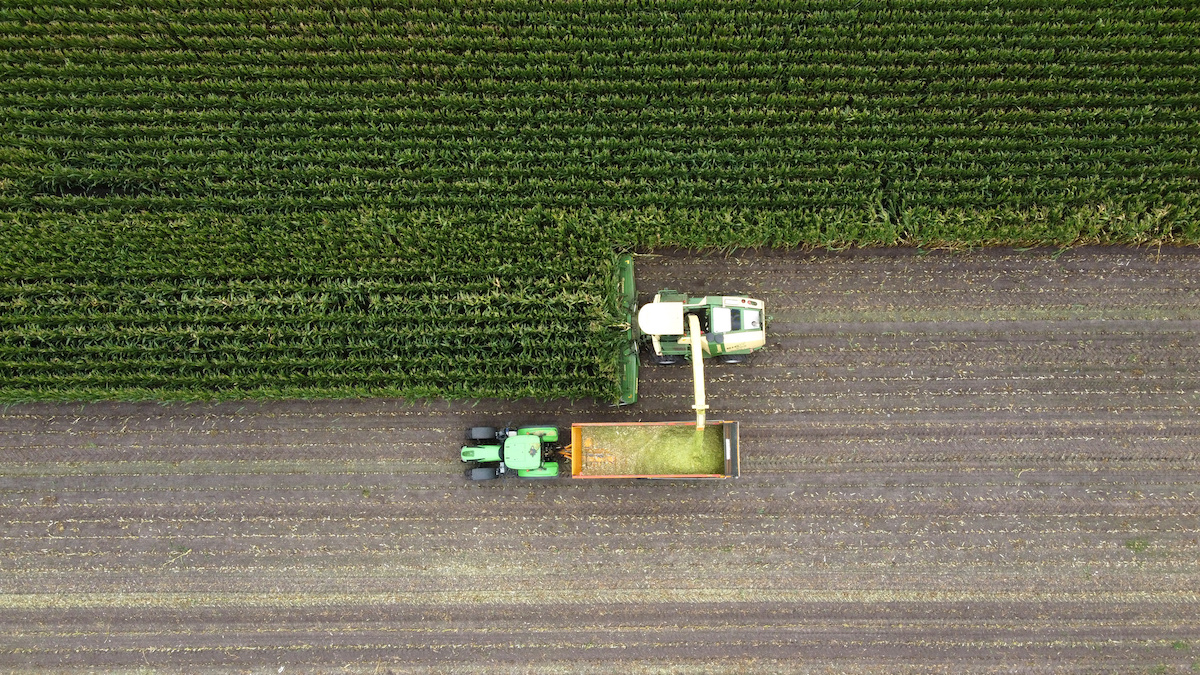
Explore the Power of Collaborative Engineering
Delve deeper into the innovative world of collaborative engineering with Lutco and see how our partnerships have led to remarkable successes in the manufacturing industry. Learn about the transformative impact of concurrent engineering methods through this real-world example, where teamwork and shared expertise unlocked new levels of efficiency and quality.
Compound Tool Design: Balancing Complexity and Cost
The same considerations apply to compound tools, where more than one operation is performed during the press cycle. It is important for the tool designer to understand the customer’s needs to avoid creating an expensive, over-engineered tool. The cost of tooling is typically charged upfront, although overseas metal stampers tend to amortize this cost in the piece price. Either way, it is a cost to the customer that must be considered during the design stage.
Predictive Maintenance Is The Key to Uninterrupted Productivity
Another key factor is “predictive maintenance” (PM) for high-volume tools. These tools must perform reliably to meet customer needs and prevent assembly line downtime due to tool breakage. Subject to high impact loads, these tools have multiple components, each with its own fatigue life (springs, punches, bolts, pilots, dies, etc.)
At Lutco, high-volume tools are monitored in a PM program, where the number of hits is recorded and maintenance and component replacement are scheduled at predetermined intervals. The main goal is to have the tool ready and reliable for the next customer order by predicting replacement and refurbishment needs before part failure can occur. This technique ensures maximum value is extracted from the tooling while avoiding the expense of unanticipated downtime.
Innovative Metal Stamping Tools Merge Tradition with Technology
Lutco excels in designing progressive and compound tools for metal stamping, blending quality with cost-efficiency through decades of metalforming expertise. Our tools, adaptable for a variety of operations, are tailored to the specific needs of each project, considering factors like part complexity and production volume. The implementation of our predictive maintenance (PM) program ensures longevity and reliability, particularly for high-volume production tools.
Our commitment at Lutco is to work closely with our clients from the start, ensuring that each tooling solution aligns perfectly with their requirements. With over 70 years of experience, we are dedicated to driving customer success.
Looking for top-tier metal stamping tool solutions? Contact Lutco today!
Our team, backed by decades of expertise, is ready to partner with you to achieve your project goals. Your success is our priority. Connect with us now for exceptional service and results.