Lutco has always been a company driven by a passion for problem-solving. While other component manufacturers may offer bearings or metal stamping, Lutco provides solutions that stretch beyond the sale of a simple part to address the function and application of the component, extend the lifetime of equipment, and reduce cost whenever possible. For one major OEM, this dedication to innovative metal solutions resulted in a complete redesign of an agricultural equipment component that would improve performance and be lighter in weight— and cost— than the original design that had brought them to Lutco in the first place.
Combine Unloader Auger Bearing Redesign Reveals Potential for Improved Efficiency and Cost Reduction
When this well-known agricultural equipment manufacturer contacted our sales engineers, Lutco identified an opportunity to develop an innovative product enhancement for a hangar bearing used in a combine auger. The redesigned hangar bearing would increase the grain flow rate through the auger tube and ultimately improve harvesting efficiency. Another benefit of the new design was a reduction in weight, making it significantly lighter than the current assembly and improving overall fuel efficiency. As an additional benefit, the redesigned unit price was lower than the cost of the previous iteration, resulting in total cost savings for the customer.
As fuel prices continue to rise, manufacturers worldwide have been compelled to seek new ways to improve their machines’ fuel efficiency. Farm equipment is no exception, as farmers are often operating on slim margins. Enticed by a design revision that would make their product more attractive to customers while reducing production cost, the agricultural OEM worked with Lutco to develop the next generation of their unloading auger bearing.
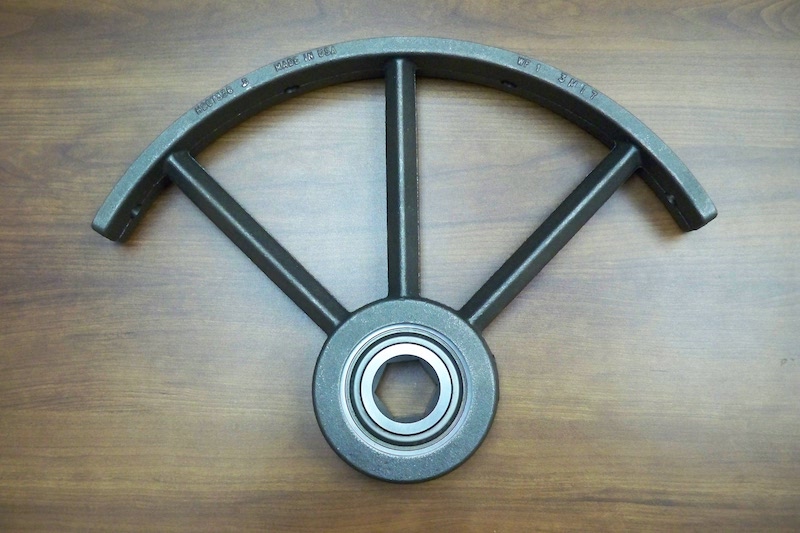
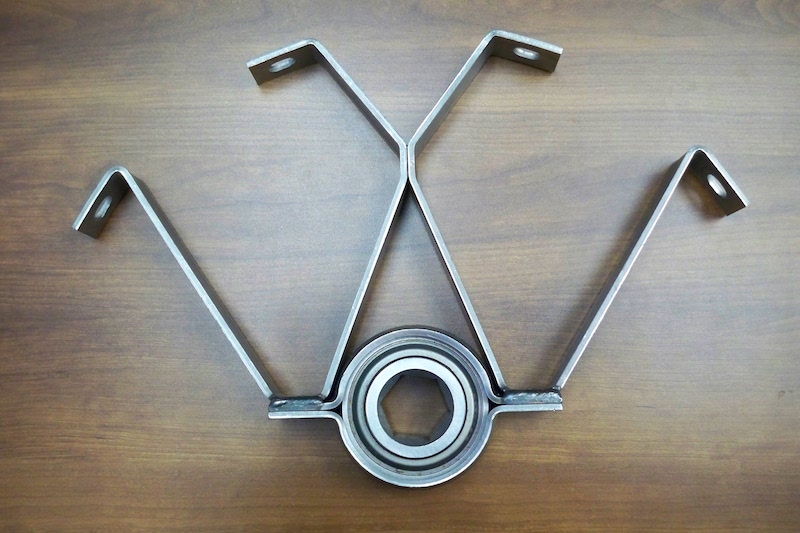
The original design utilized a hex bore bearing pressed into a cast housing. Lutco’s revised auger bearing design incorporated the same hex bore bearing as in the initial assembly; however, the housing was made from heavy gauge, high strength, low alloy steel stampings. The various stamped components were configured, assembled, and welded in critical locations that maximized the assembly strength. The result was a reduced weight on the cantilevered auger and lower power required to move grain.
Collaborative Design Process Leads to Agricultural Bearing Innovation: The ‘Flying W’ Is Born
This collaborative effort brought together input from both the customer and several departments across Lutco. Design & Applications Engineering, Manufacturing, Tool Design, and Purchasing teams contributed their perspectives to develop a successful product. Regular conference calls took place with the customer’s engineering team analyzing design revisions, stress analyses, and ultimately refining the final design. Multiple variations of samples were fabricated and submitted to the customer for testing. Due to the eye-catching geometry of the new model, the product became known colloquially as ‘the Flying W.’
If this customer had chosen a low-cost, off-shore component supplier, they would have missed the opportunity to improve their product’s performance, the efficiency of their design, and the overall production cost. There are thousands of component manufacturers to choose from, but when you work with Lutco, you benefit from a more valuable collaborative relationship. For over 70 years, Lutco has been a reliable, resourceful, innovative manufacturing partner for some of the world’s most influential OEMs, and that success is based on a willingness to do whatever it takes to produce a great product. Lutco helps customers reimagine what’s possible.