A custom bearing can satisfy almost any customer’s needs. Your application may need a needle roller or ball bearing, a radial or angular contact design, a plain carbon steel bearing with anti-corrosion coatings or stainless steel, a thrust bearing or a spherical bearing, tight or loose radial play, sealed or non-sealed designs— the list can go on and on.
Bearing customization starts with an in-depth analysis and understanding of the application: loads (magnitude and direction), speeds, operating temperatures, working environment, duty cycles, acceleration, and size constraints. Design for manufacturability and assembly (DFMA) is also considered, with required tolerances, geometry, raw materials, and machine and/or press capabilities taken into account.
One might ask: “Why so much effort? Just buy an off-the-shelf bearing!” But experienced OEMs will be the first to tell you that customized bearings are well worth the effort and deliver a host of benefits all their own.
Lutco’s Top 3 Reasons For Embracing Customized Bearings
#3: Improved Performance
An application’s unique needs extend well beyond the basic type of bearing or size requirements. A customized bearing can be engineered for a particular application and its operating conditions, achieving optimal performance by enhancing the speed rating, load rating, or other parameters. When it comes to designing customized bearings, we design for what you need.
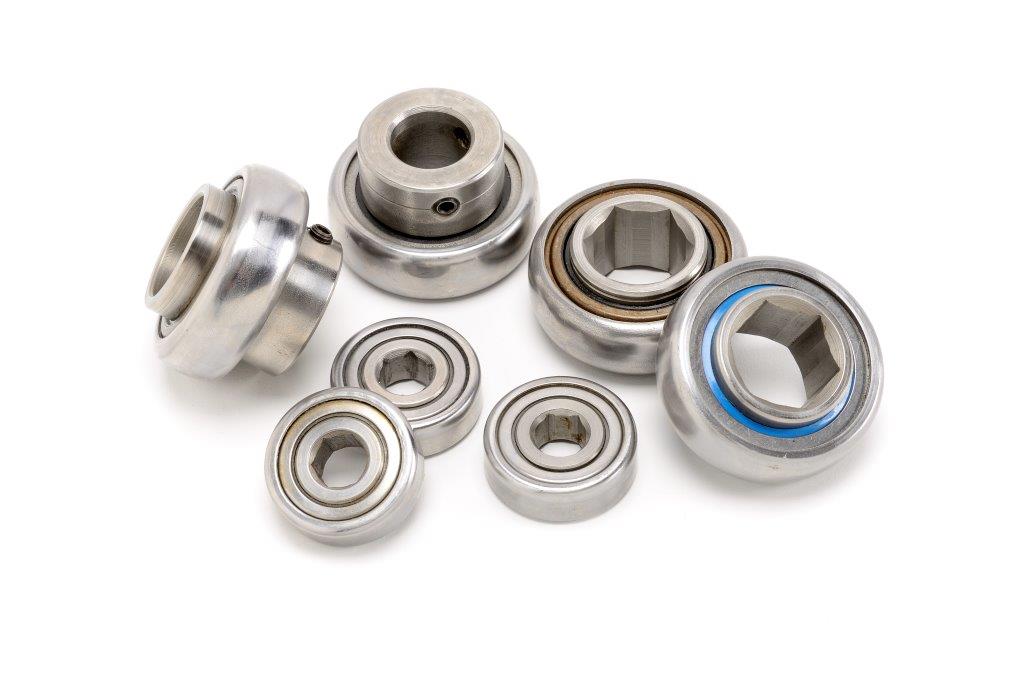
Customized bearings provide OEMs with the right bearing for their specific needs, eliminating the production time and expense required to augment standard parts.
When trying to improve performance in an application, customized bearings offer specific advantages that off-the-shelf or stock bearings can’t match.
#2: Increased Bearing Service Life
Increase service life by customizing the bearing to the operating conditions where different hardness, coatings, sealing, and geometries will aid the bearing to operate for longer periods compared to a standard bearing.
With customized bearings, you can achieve maximum efficiency and create a bearing specifically designed to achieve specific goals like noise reduction or eliminating vibration and friction. While a stock bearing may have the right footprint or corrosion resistance, finding a ready-made bearing that is perfectly attuned to your application’s specific properties is highly unlikely.
Bearings designed to fit the ‘most common’ operating scenarios have a higher probability of premature wear or failure due to the concessions and compromises you’ll have to make on the features that differentiate your application.
#1: Cost Reduction
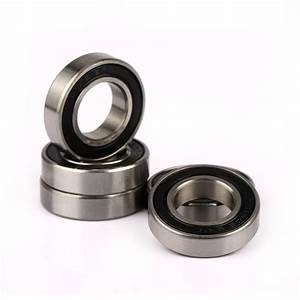
Off-the-shelf bearings typically require some aftermarket customization to meet an application’s needs.
Off-the-shelf or ‘stock’ (standard) bearings are designed to be mass-produced; they fit standard housings, have a standard inner ring width, and so on. Customized bearings are not mass-produced, which means a bearing with custom features is likely to display a higher per-part price tag than stock or off-the-shelf versions of the same part. However, custom bearings offer many cost-saving benefits that drive down operating costs and minimize downtime caused by bearing failure.
Most high-volume bearing manufacturers offer a standard design or range of designs, relying on economies of scale to keep pricing at an absolute minimum while still turning a profit. But this forces their customers to either augment the part in-house or reengineer the machine design to accommodate it, which can drive the per-piece cost well beyond the initial “savings” achieved by specifying a stock part in the first place.
Customized bearings don’t require special housings, shafts, or other changes for mounting them into the subassembly or the final unit. The lengthy list of augmentations and aftermarket customizations incurred by stock bearings don’t just add complexity or potential failure points, they also increase the BOM compared to an integral customized subassembly and drive up labor costs at each step of the way— not to mention the additional engineering time to come up with solutions for problems that never needed to exist in the first place!
Customized Bearings Tailored To Your Application’s Unique Demands
At Lutco, specialized modeling software, engineering expertise, and technical know-how combine to design, fabricate, and assemble the optimal bearing for your needs. Concurrent engineering practices allow our toolmakers and engineers to communicate in real-time, facilitating cooperative process development while maximizing design efficiency.
Working with a manufacturing partner that can offer engineering, toolmaking, production, and assembly under one roof means faster, more efficient operations, reduced shipping costs, and tighter security around your IP.
With customized bearings, you get the best of both worlds: customized design that delivers maximum performance and the assurance that your bearing is designed, produced, and assembled by experts. The superiority of customized bearings means lowered maintenance costs, lower operating expenses, and less downtime due to bearing failure – so consider how working with the Lutco team to develop the best solution for your application could save you time and money.
Do you have a new bearing application or need cost savings on an existing one?
Speak with Lutco’s engineers today to learn how customized bearings can help you achieve that goal.