Lutco recently took on a customer that needed a vendor who could deliver fast turnaround times producing conical cutters from an exotic steel alloy. The process required metal stamping, drawing, and heat treating. Despite tight timelines and no tooling documentation available, Lutco managed to successfully complete the job while gaining valuable knowledge and experience along the way.
Reverse Engineering and Modifications Improve Service Life of Cutters
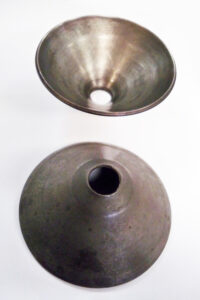
In lieu of detailed documentation, Lutco’s engineers carefully inspected tooling and parts to reverse engineer and eventually improve the production process for these conical cutters.
The engagement between Lutco and the customer was the result of a local metalforming vendor, who was relocating and exiting the stamping business and wanted to find a reliable source for their customer before their departure. Due to the complexity of the multi-stage process required to produce the part, they referred the job to Lutco.
As is often the case when inheriting a legacy part from a long-term vendor relationship, there were some gaps in the documentation. While part prints were available, tooling prints were not, and the previous engineers had all moved on to new job roles following the closure of the company. To resolve this, Lutco’s engineering team set to work reverse engineering and creating all of the necessary documentation for each stage in the process, ensuring that production could move forward. This detailed analysis was expedited by clear and responsive communications with the customer throughout the process.
Lutco’s team examined the customer’s part sample and applied their expertise to reverse engineer the process. Lutco determined that the production of this unique part could be accomplished using heat treating, metal stamping, and drawing processes. The material, 6150 CRS, is a high-carbon chromium-vanadium steel alloy with higher strength and hardness that would require expert handling to produce a high-quality part. Using a combination of experience, metalforming expertise, CAD modeling software, and other engineering tools, Lutco was able to develop a complete set of tooling to produce conical cutters from the exotic steel alloy requested by the customer.
Heat Treating & Metal Stamping: A Recipe for Success
Metal stamping & drawing processes, heat treatment, and annealing (after each draw operation) were used in production to successfully produce the conical cutters that would be used in the customer’s manufacturing plants. In addition to the recreation of the previous vendor’s process, Lutco suggested modifications to the main shafts in order to increase the service life of the conical cutters, which had experienced some cracking and premature failure.
Heat treating stamped metal parts involves the application of high temperatures to harden parts and improve their wear resistance. To achieve the desired results, Lutco had to adjust the heat-treating process for this particular steel alloy. This included heating the parts above their recrystallization temperature before cooling them slowly in order to reduce their hardness and increase ductility. Lastly, annealing was used to increase toughness, reducing brittleness and increasing strength.
The Experts at Lutco Deliver Despite the Challenges
In conclusion, this project was a great success for Lutco. Despite the challenges, the job was successfully delivered within 4 months. Through reverse engineering and modifications made on the main shafts in order to increase service life of cutters, Lutco was able to successfully deliver conical cutters that met the customer’s requirements while gaining valuable knowledge and experience for future customer engagements.
Ready to see what Lutco can do for you?
Reach out today to learn more about our process and capabilities.